Table of contents
The digital revolution has transformed countless industries, and the world of textile manufacturing is no exception. The advent of innovative digital spinning platforms has opened up a plethora of opportunities, optimizing production processes and enhancing product quality. As we delve into the myriad benefits these platforms offer, readers will gain insight into how technology is redefining the future of fabric creation. Join us as we unravel the advantages that make digital spinning a key player in the textile industry's ongoing evolution.
Revolutionizing Textile Production
The integration of innovative digital spinning platforms is transforming the textile industry at an unprecedented pace, enhancing textile production efficiency to meet the demands of a rapidly evolving market. By leveraging the power of digital spinning optimization, manufacturers are able to streamline their operations, leading to significant improvements in the speed and quality of yarn production. These platforms enable factories to reduce manual errors and inconsistencies, ensuring products meet high standards of quality.
Furthermore, one of the standout advantages of such platforms is their contribution to reduced waste in textiles. By fine-tuning production parameters and monitoring for deviations, digital spinning platforms ensure that materials are used judiciously, minimizing scrap and promoting sustainable manufacturing practices. This not only reduces the environmental footprint of textile production but also enhances the cost-efficiency of operations.
Predictive maintenance, powered by data analytics in spinning, is another vital feature that underlines the efficacy of these platforms. By analyzing machine performance data, these systems can forecast when maintenance is required, preventing unexpected downtime and prolonging the lifespan of the machinery. This predictive approach allows for seamless production flows and reduces the likelihood of costly disruptions.
The role of automation in this context cannot be overstated, as it is the cornerstone upon which the efficiency and reliability of digital spinning platforms are built. Automation ensures that repetitive and complex tasks are handled with precision and consistency, freeing up human operators to focus on overseeing the production process and making strategic decisions.
A prime example of how brands are harnessing these advancements is Spinwiz. Their state-of-the-art solutions are exemplary in showcasing how digital spinning platforms can revolutionize textile production, setting new standards for efficiency and innovation in the industry.
Enhancing Product Quality and Consistency
The advent of digital spinning platforms has revolutionized the way textiles are produced, significantly contributing to the yarn quality consistency and fabric production uniformity. Through precision in spinning, these sophisticated systems offer unparalleled control in textile manufacturing, ensuring that each thread meets strict standards. The tension, weight, and tensile strength of the yarn are meticulously monitored and controlled, leading to products of remarkable and consistent high quality. One notable advantage is the substantial reduction in human error, which is pivotal in maintaining high production standards, especially when dealing with large volumes. Consequently, digital spinning platforms have become indispensable in the textile industry, underpinning a solid foundation for reliability and excellence in fabric production.
Creating Sustainable Solutions
The advent of digital spinning platforms heralds a transformative era for sustainable textile production. Such technological advancements are paving the way for energy-efficient spinning processes that promise to substantively curtail energy consumption within the industry. A noteworthy aspect of these platforms is their capacity for resource waste reduction, enabling manufacturers to minimize their environmental footprint. As the textile sector grapples with the challenge of integrating eco-friendly fabric innovations, digital spinning platforms stand as pillars of progress, facilitating the use of recycled materials in textiles with greater ease and efficiency.
These innovative systems offer the flexibility to swiftly incorporate advancements in sustainable raw materials, ensuring that the textile industry remains at the forefront of green manufacturing practices. Moreover, the integration of life cycle assessment tools within digital spinning platforms allows for a comprehensive evaluation of environmental impact, underscoring the commitment to ecological stewardship from the fiber's creation to the final fabric. The culmination of these factors underscores the role of digital spinning technologies as instrumental in forging a more sustainable and responsible textile industry for future generations.
Customization and Flexibility in Design
The advent of digital spinning platforms has revolutionized the textile industry, providing unprecedented customization benefits. These platforms empower designers and manufacturers with the ability to effortlessly adjust a multitude of parameters, paving the way for bespoke yarn creation that perfectly aligns with intricate customer specifications. The scope of custom textile design has been broadened significantly, allowing for a seamless transition from traditional patterns to groundbreaking and personalized fabric compositions.
With the introduction of flexible fabric production, the door has been opened to a world where experimenting with various fibers, blends, and patterns is not only possible but also encouraged. This has led to the development of innovative fiber blends that were once deemed unattainable. The digital spinning customizability extends beyond mere aesthetics, influencing functionality and performance traits of the yarns and fabrics produced. Moreover, digital patterning stands out as a technical term that encapsulates the essence of this modern approach, highlighting the precision and variety that can be achieved through digital means.
The capabilities of these platforms do not merely stop at the ease of creating diverse textile designs; they also offer a flexibility that traditional methods cannot match. Designers can now swiftly pivot between projects, test new ideas, and refine designs with minimal waste and time, thanks to the streamlined process provided by digital spinning technologies. In essence, the fusion of technology and textile expertise has led to a new era of fabric production where the limits are defined only by the imagination of the creators.
Integrating with the Digital Ecosystem
The incorporation of digital spinning platforms into the broader digital ecosystem marks a transformative shift in the textile industry. These innovative systems serve as a linchpin for enhancing manufacturing process connectivity, seamlessly interfacing with an array of digital tools and systems. By fostering digital ecosystem integration, these platforms enable a more cohesive and responsive operational flow. They can exchange data with supply chain management software, ensuring real-time inventory tracking and material sourcing, which optimizes the supply chain's efficiency. Furthermore, connectivity with textile e-commerce platforms permits an agile response to market demands, facilitating quicker product launches and adaptation to consumer preferences.
Through end-to-end digital solutions, businesses within the textile sector can achieve unprecedented levels of transparency and control over their manufacturing processes. This harmonization is emblematic of Industry 4.0, where the fusion of physical production with smart digital technology paves the way for a more intelligent, interconnected manufacturing environment. Such integration allows for predictive maintenance, enhanced quality control, and more agile decision-making, leading to better resource management and reduced waste. In essence, the synergy between digital spinning platforms and the digital ecosystem embodies the next generation of industrial proficiency, propelling the textile industry toward a more innovative and sustainable future.
On the same subject
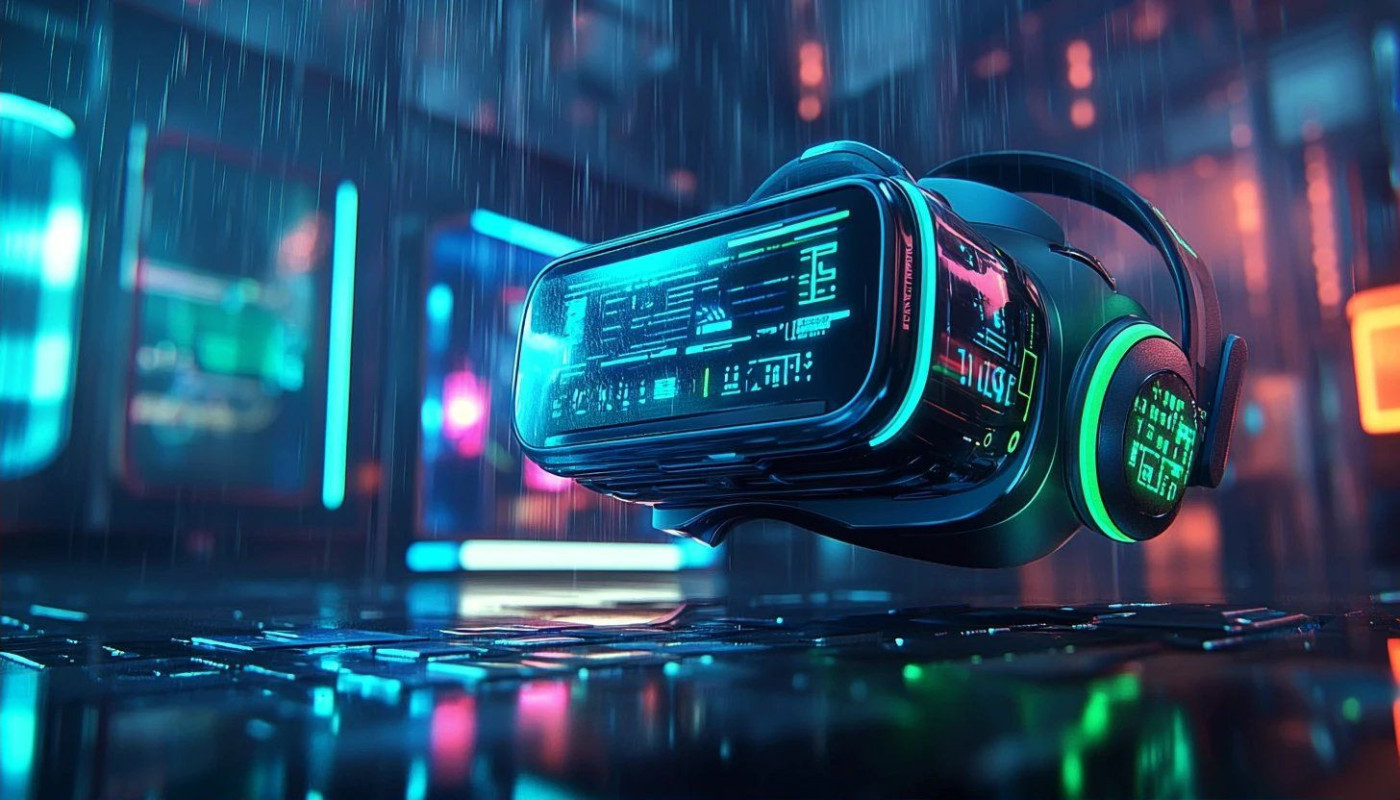
Exploring The Rise Of Low Deposit Options In Online Gaming
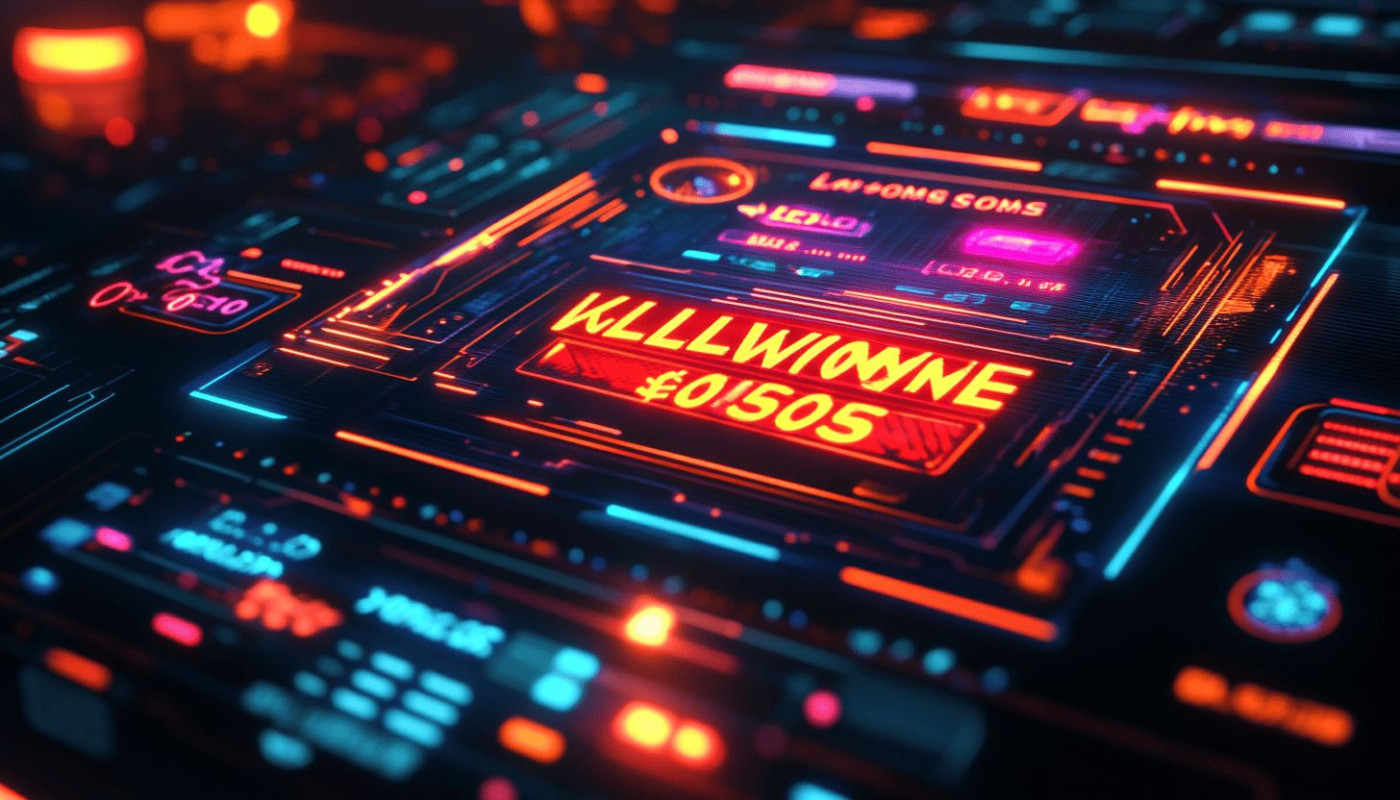
Exploring The Benefits Of Welcome Bonuses In Online Gaming Platforms
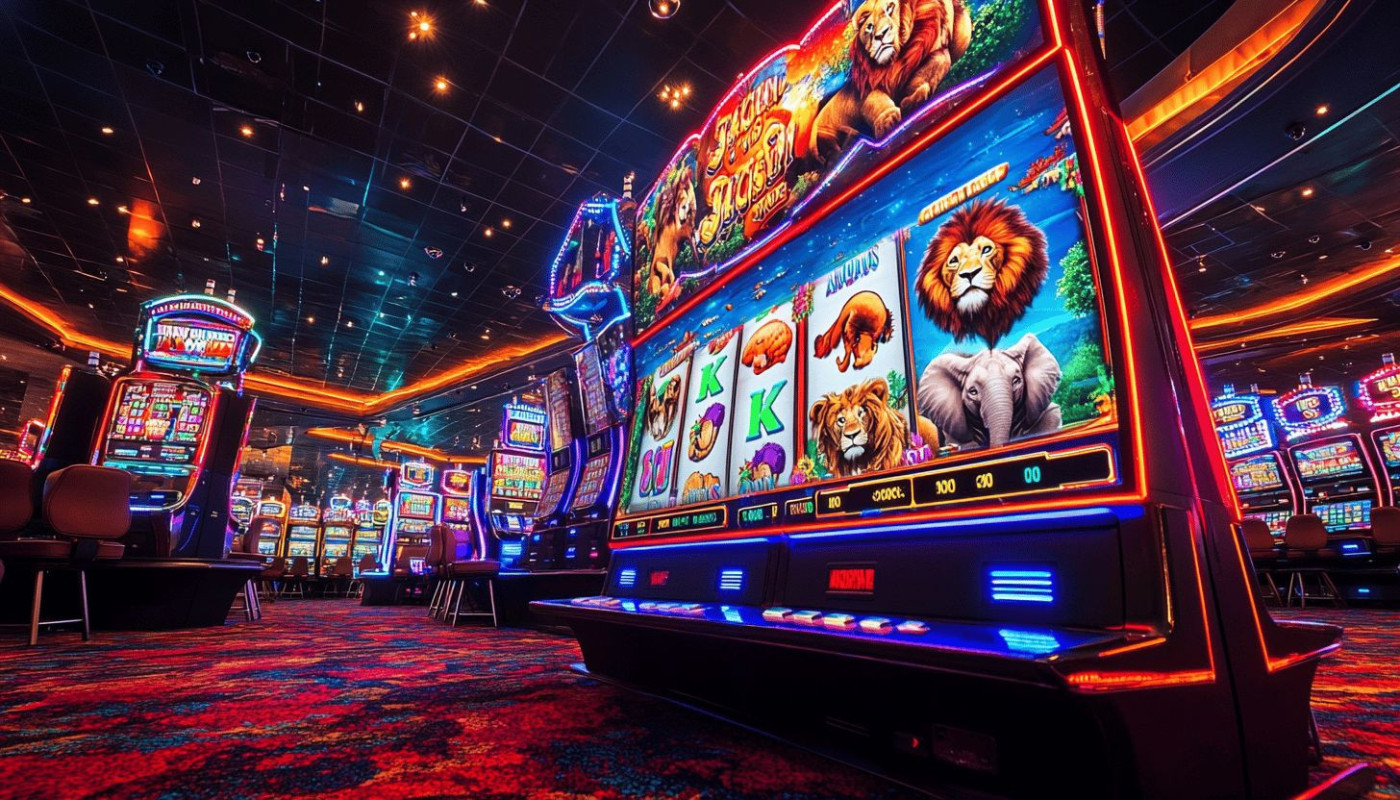
Exploring The Popularity Of Animal-Themed Casino Games

Comparative Analysis Of PC Games Adapted From Iconic Comic Series
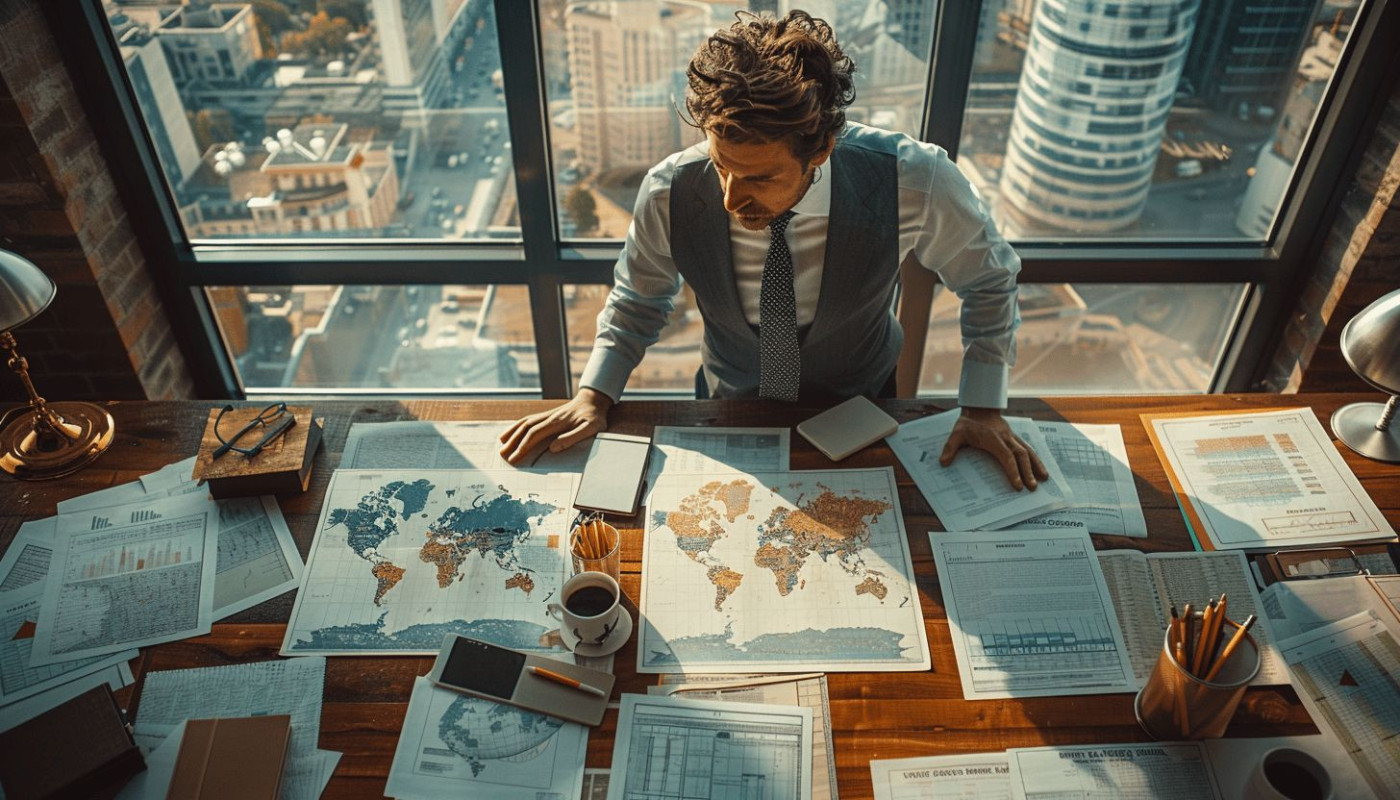
Exploring The Legality Of Binary Options Trading Worldwide

Mobile Compatibility: A Must-Have For Modern Online Casinos
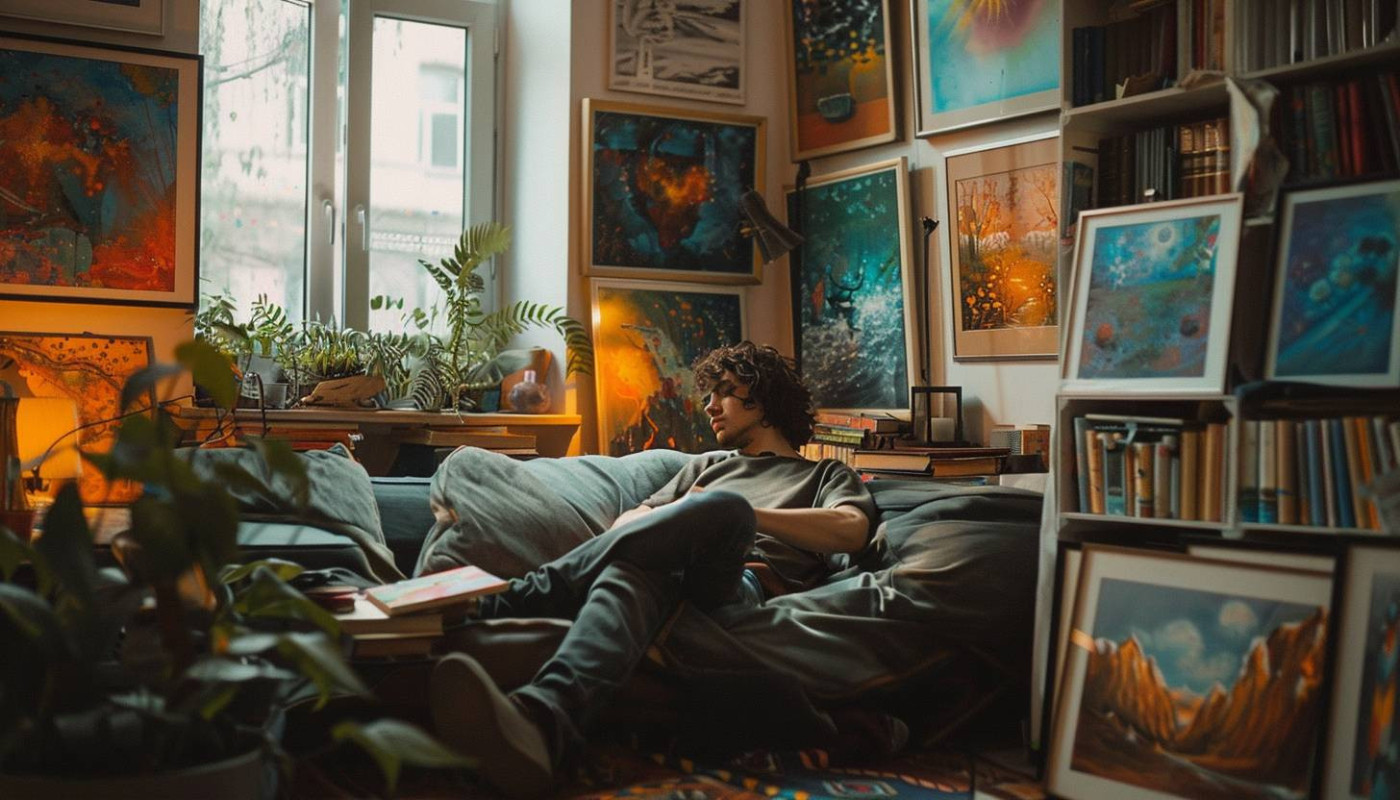
Exploring Effective Tactics For Enhancing Personal Connections And Hobbies
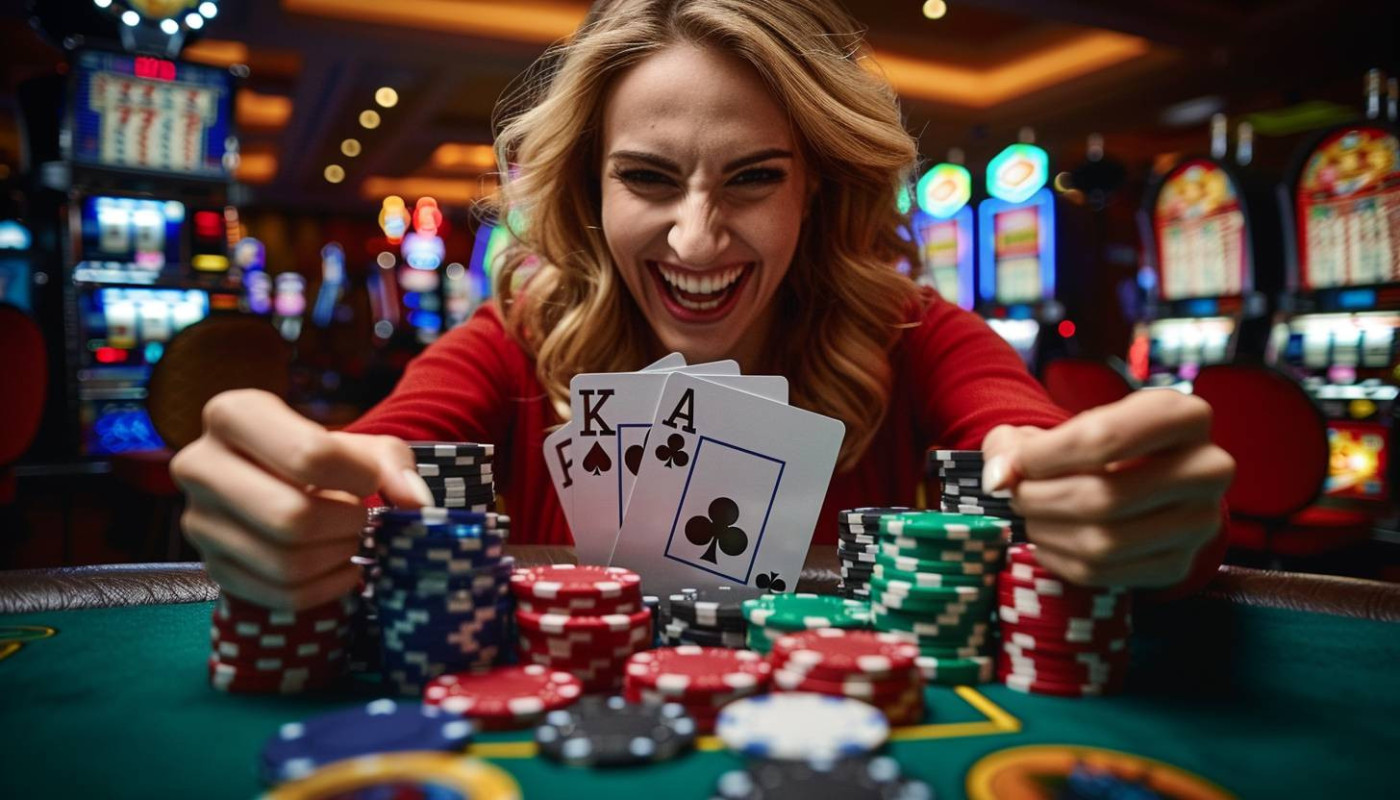
Exploring The Benefits Of Online Casino Bonuses And Promotions
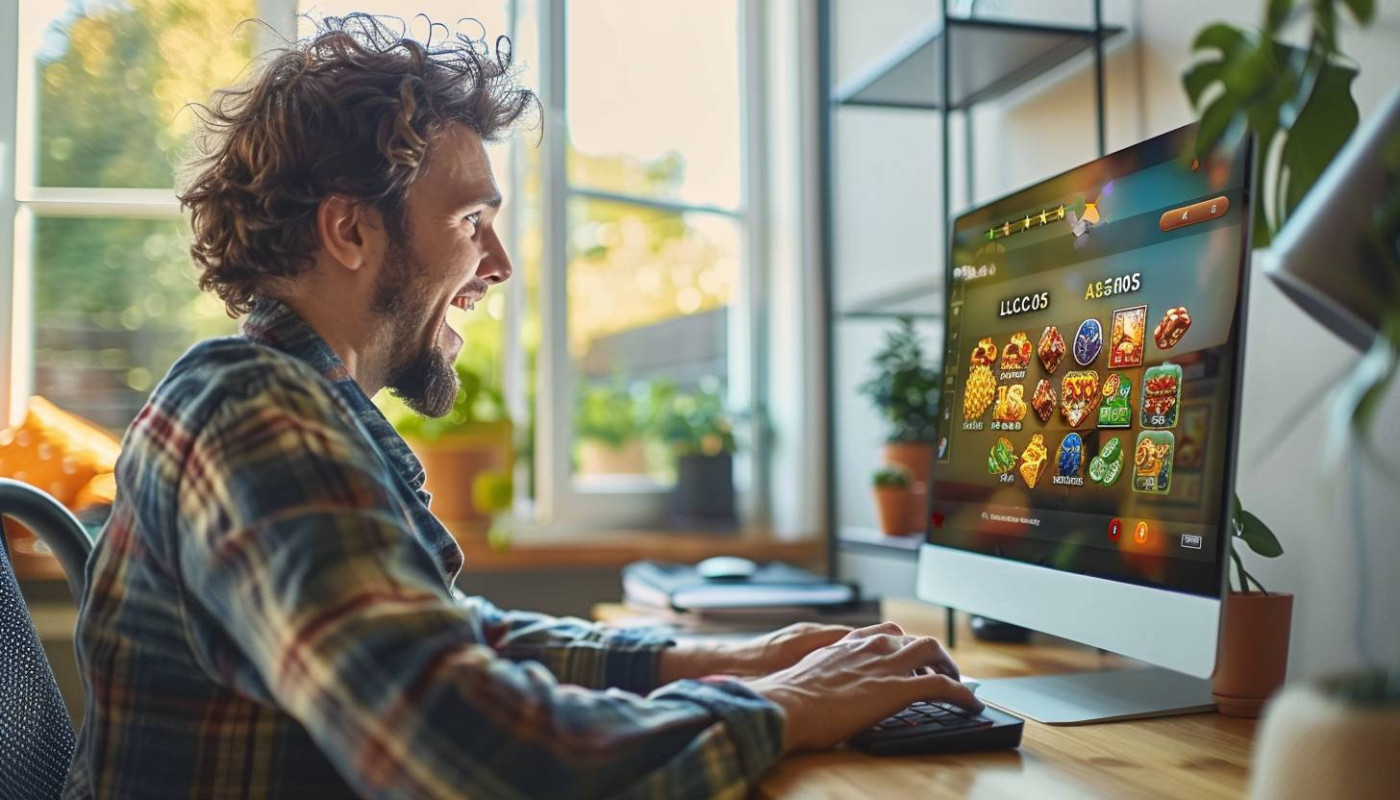
Maximizing Your Benefits With Welcome Bonuses And Free Spins
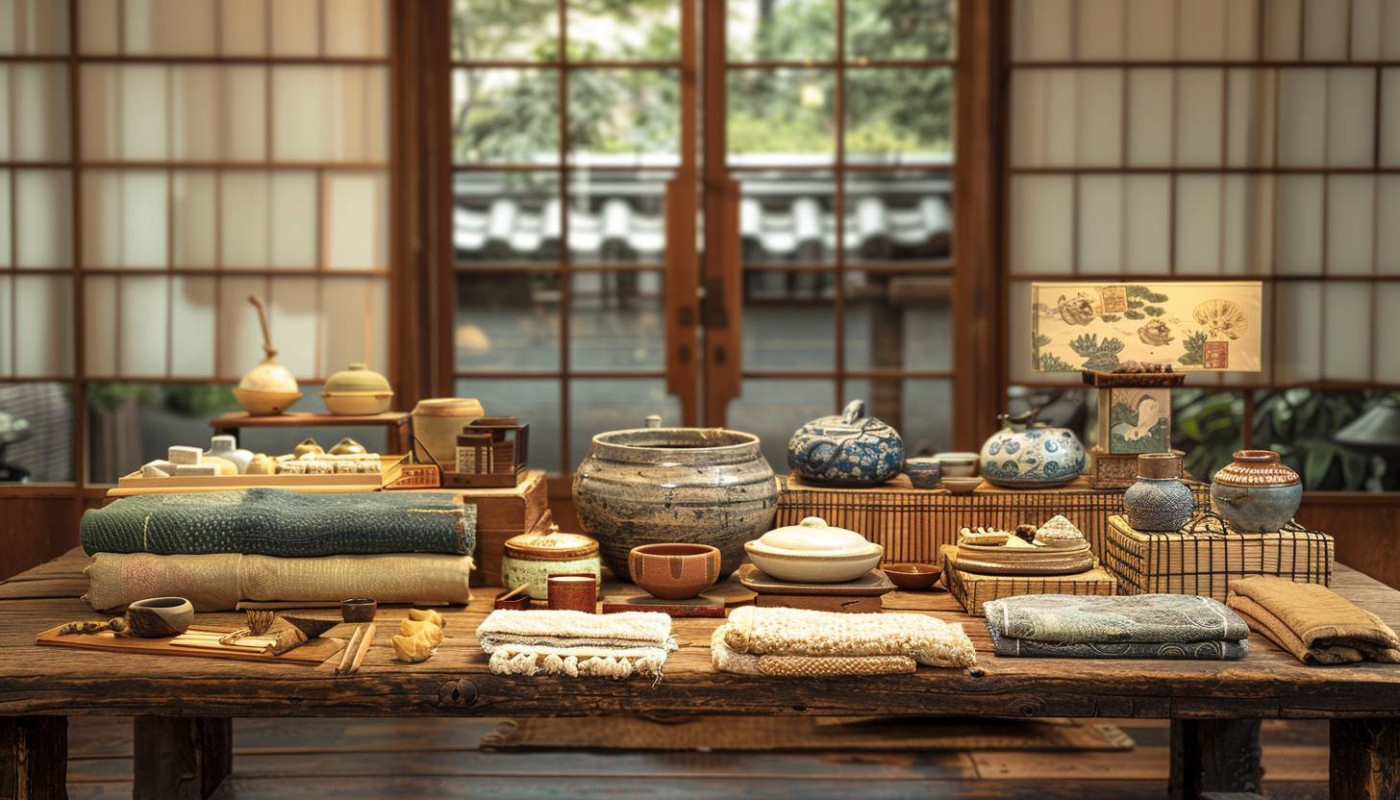
Exploring Traditional Japanese Crafts Through Modern E-commerce Platforms
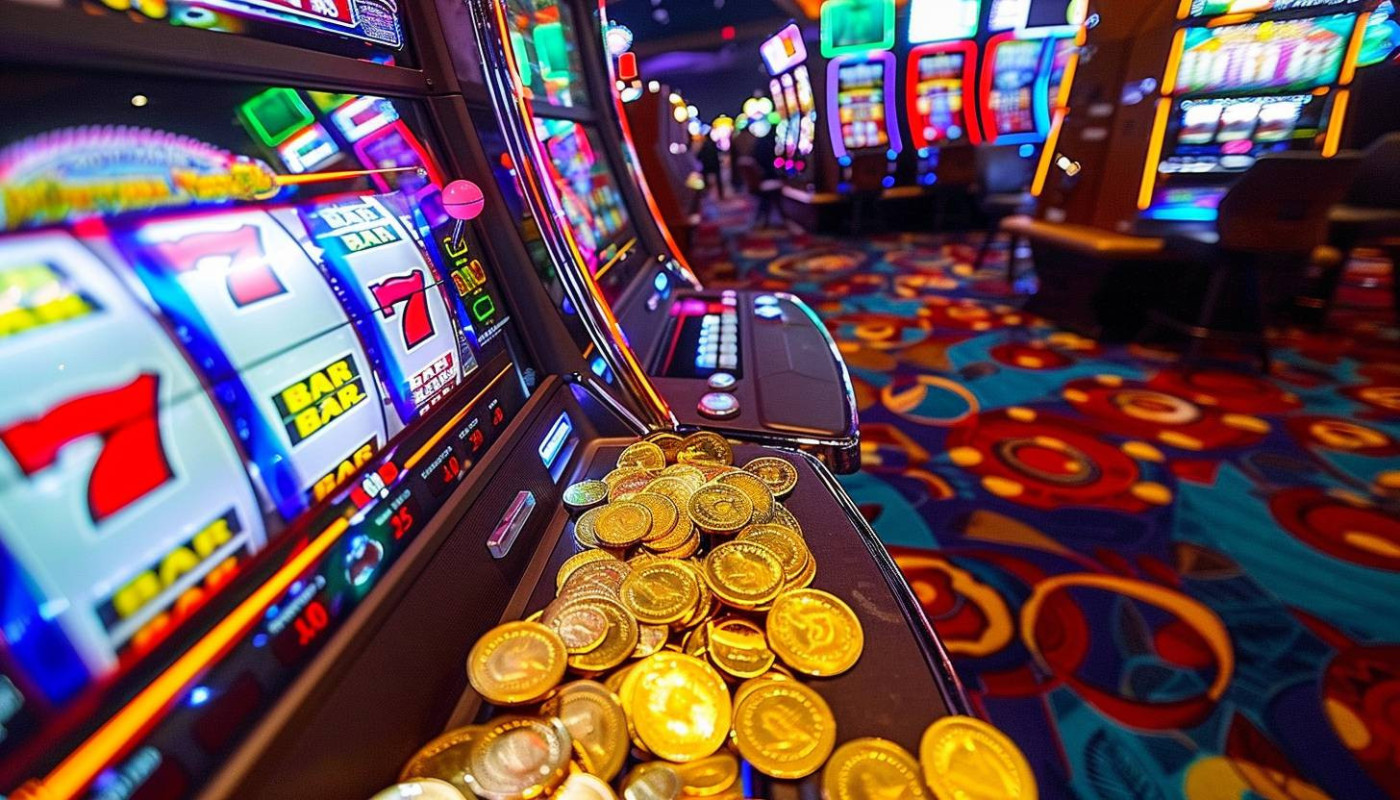
How To Maximize Winning Chances On High Volatility Slots
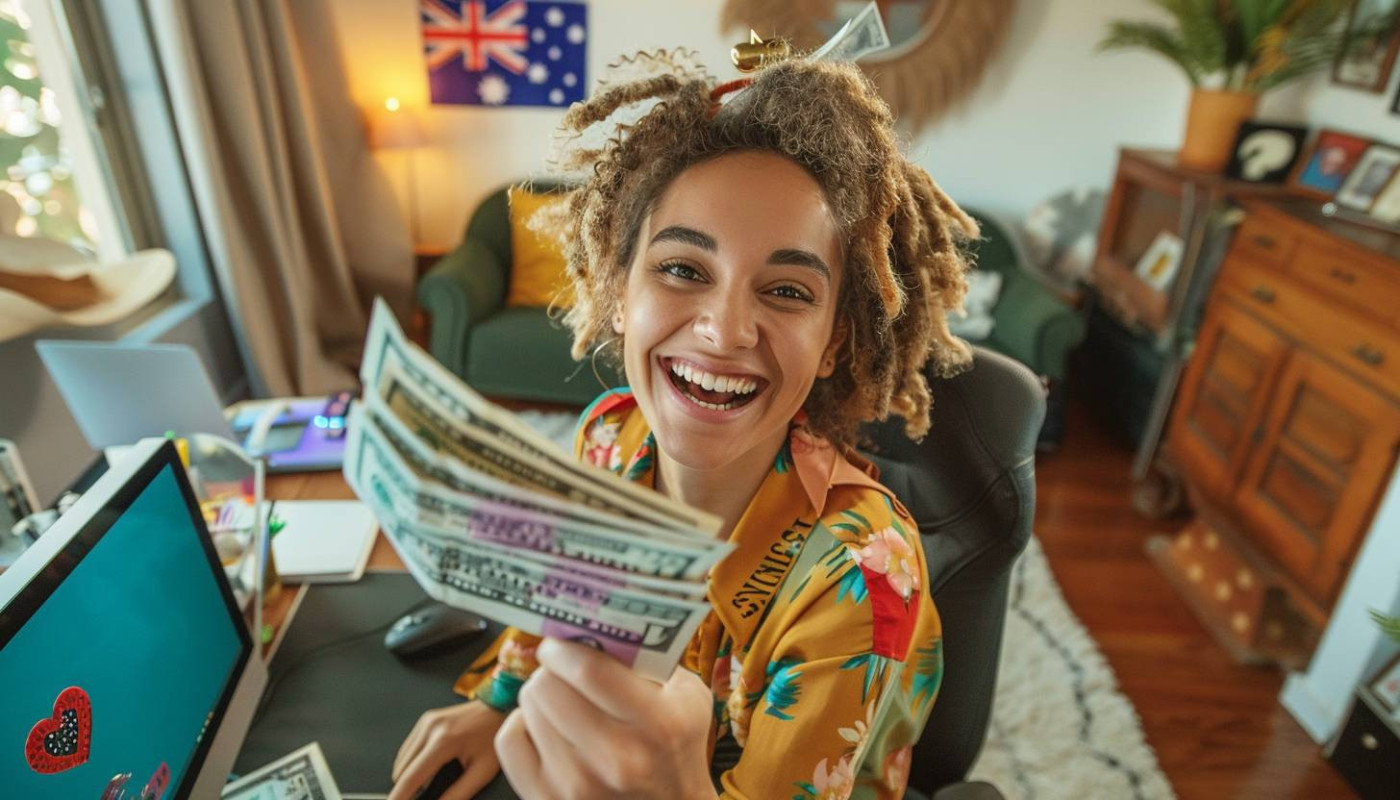
Personal Stories Of Winning Big In Australian Online Casinos
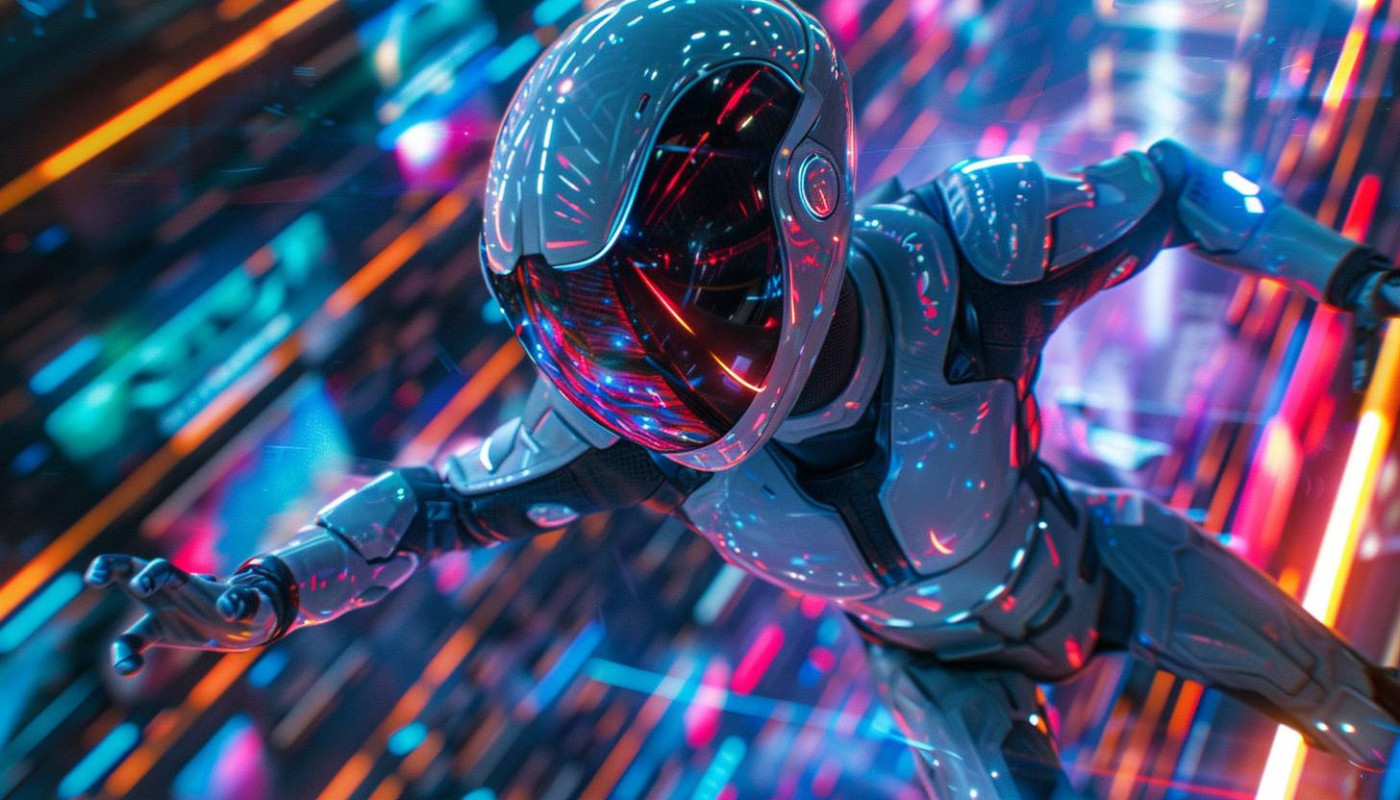
Exploring The Future Of Online Gaming And Technology
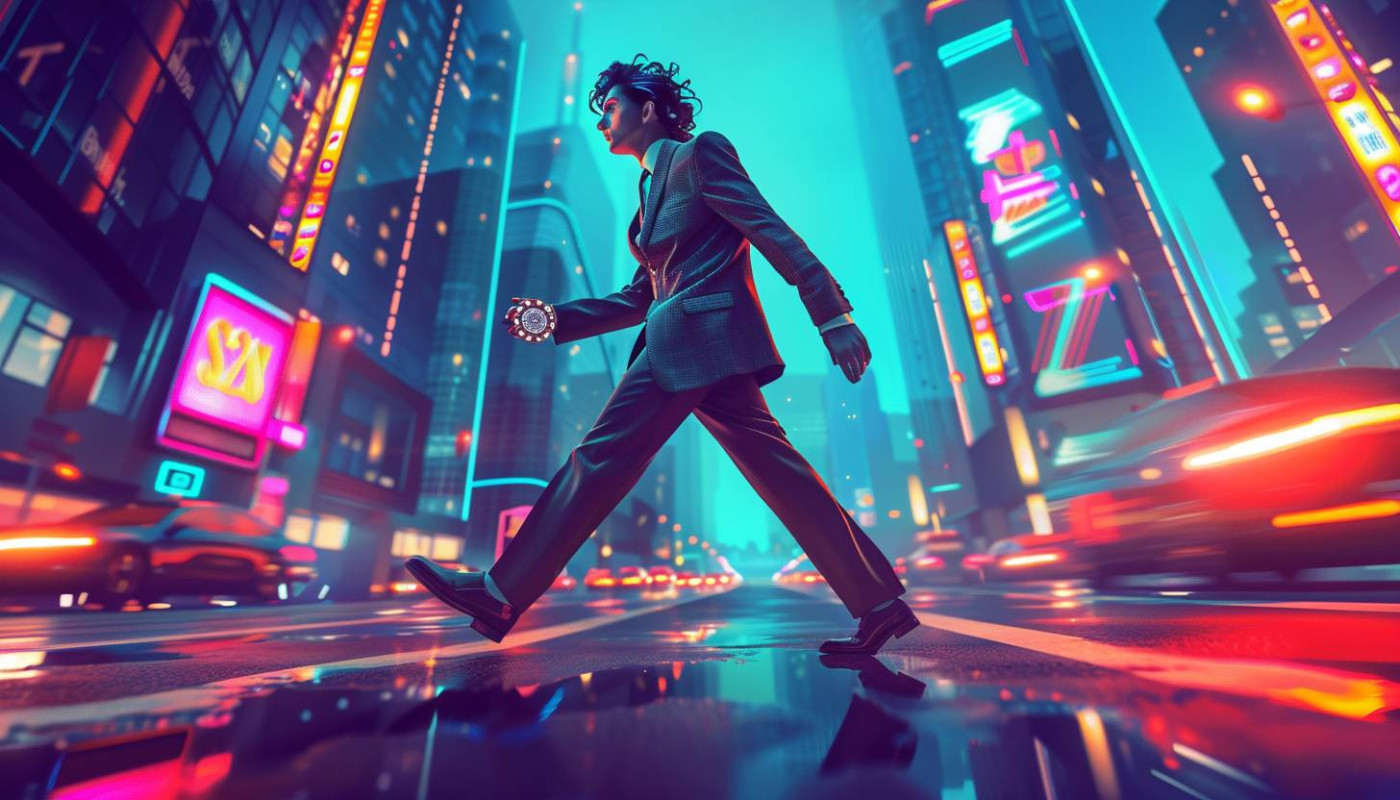
Exploring The Thrill Of A Virtual Road-Crossing Casino Game
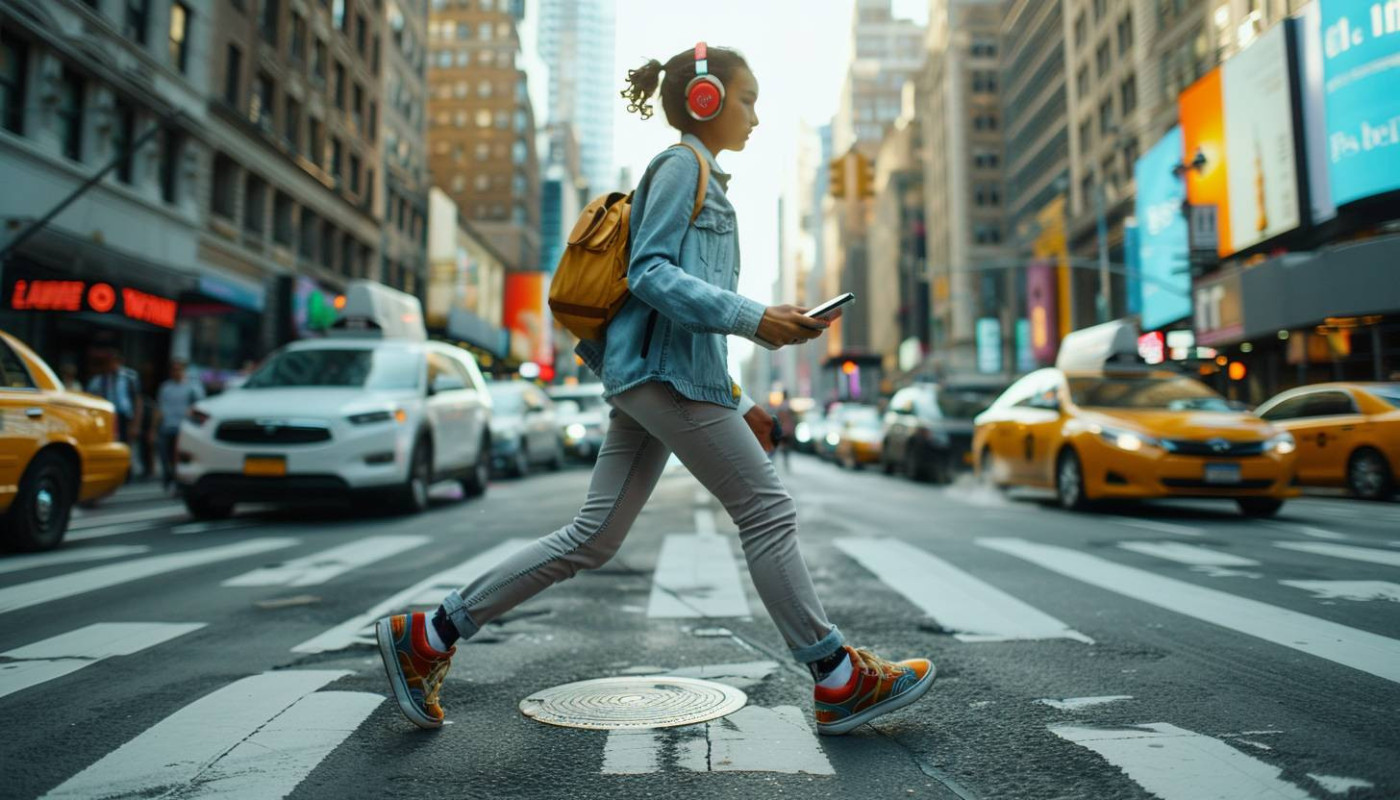
Playing Road Crossing Games On Mobile: Tips And Tricks
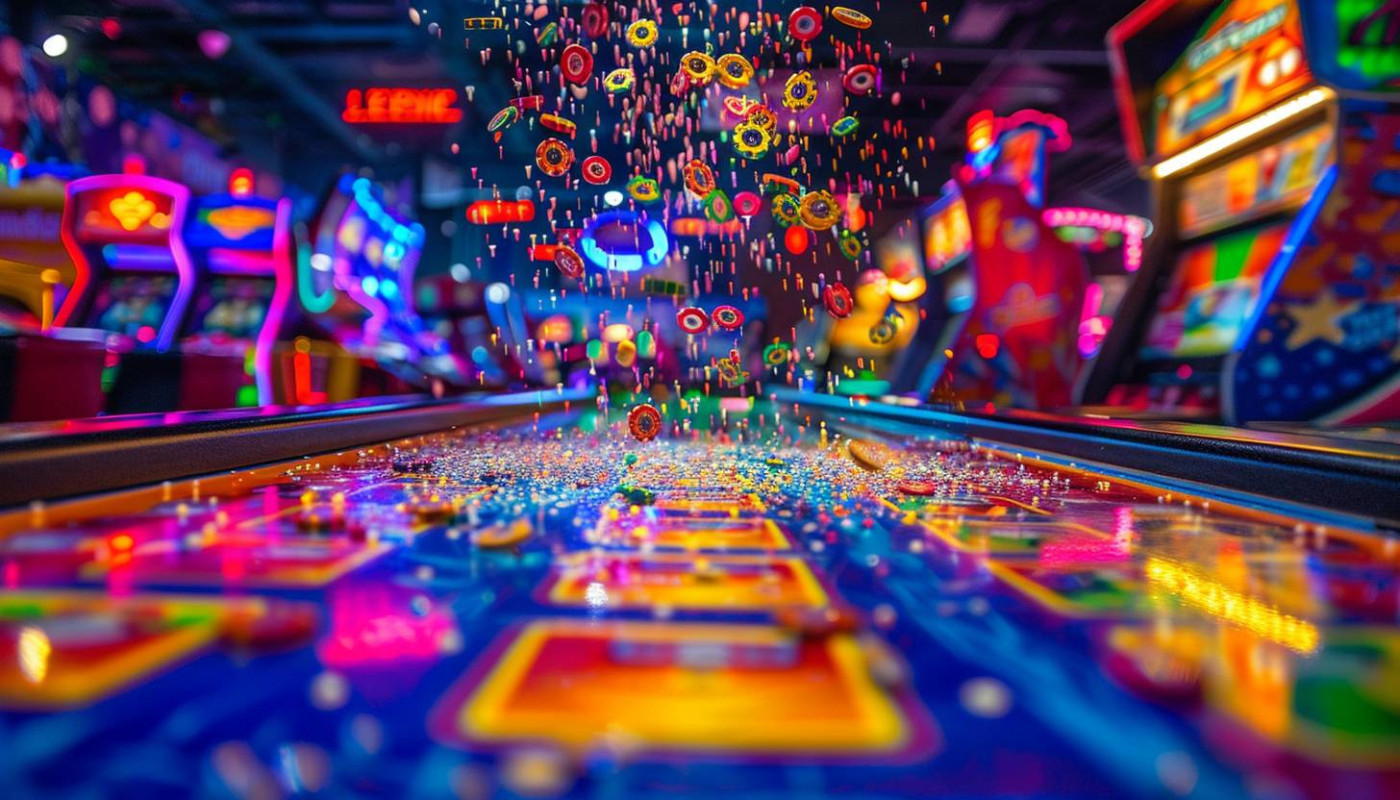
Strategies For Maximizing Winnings In Online Plinko Games
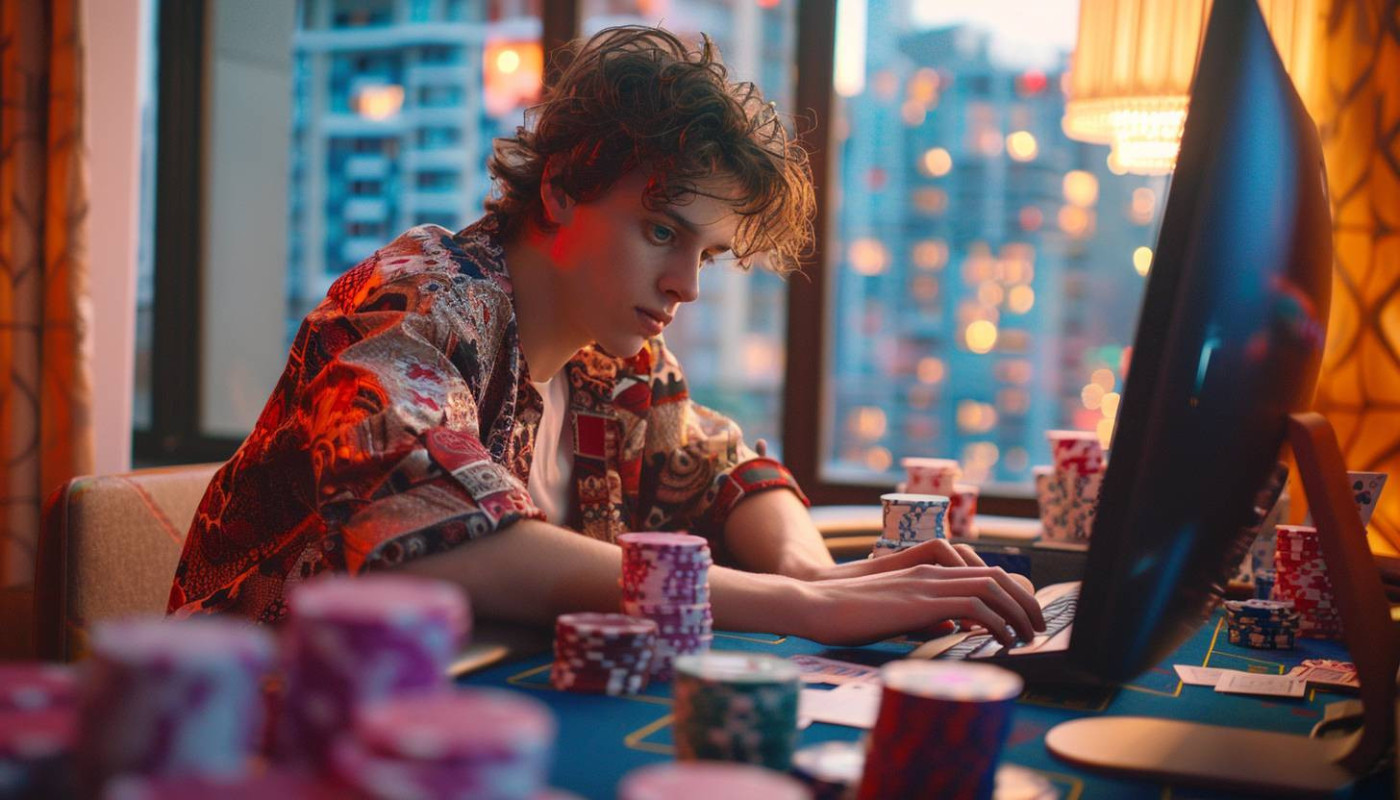
Exploring The Benefits Of Low Deposit Options At Online Casinos
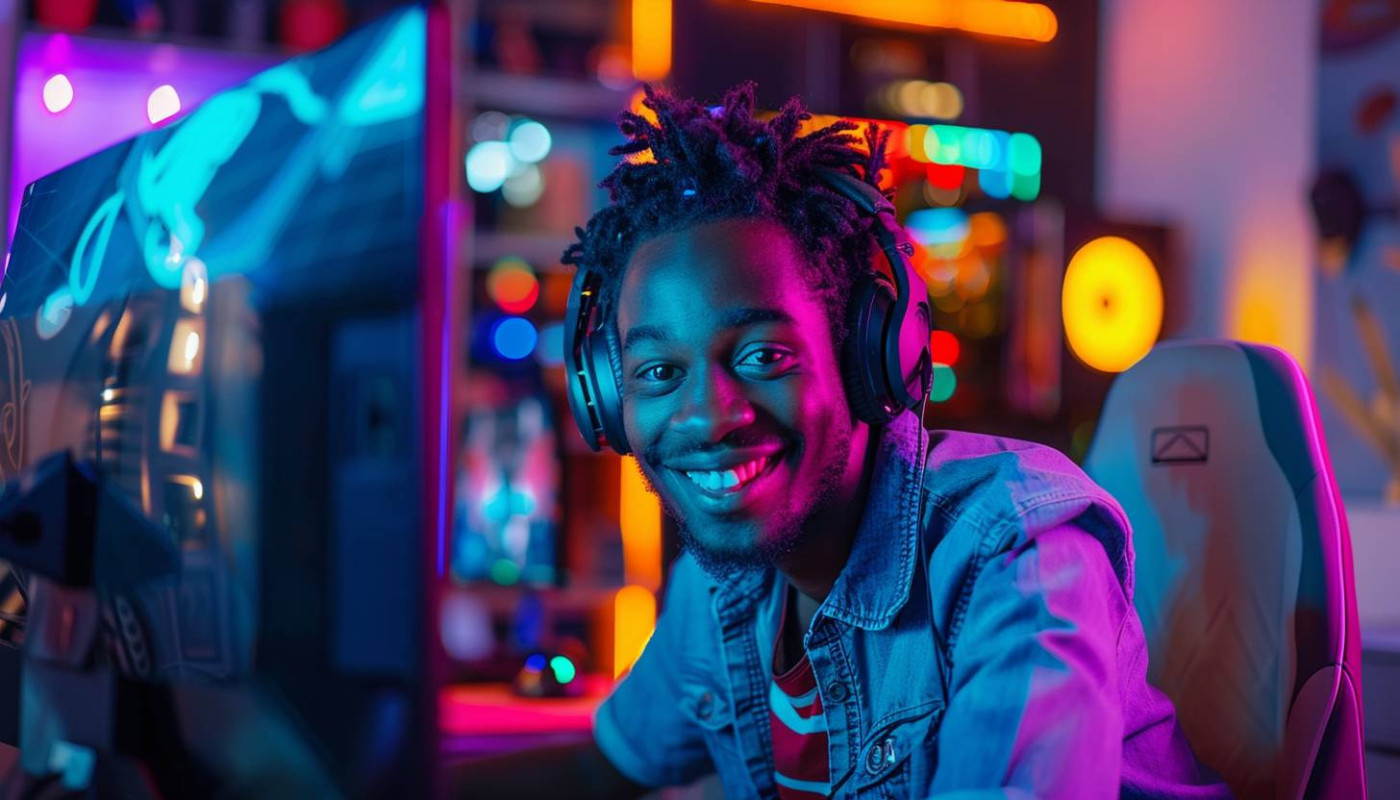
Exploring The Benefits Of Generous Sign-Up Bonuses In Online Gaming Platforms
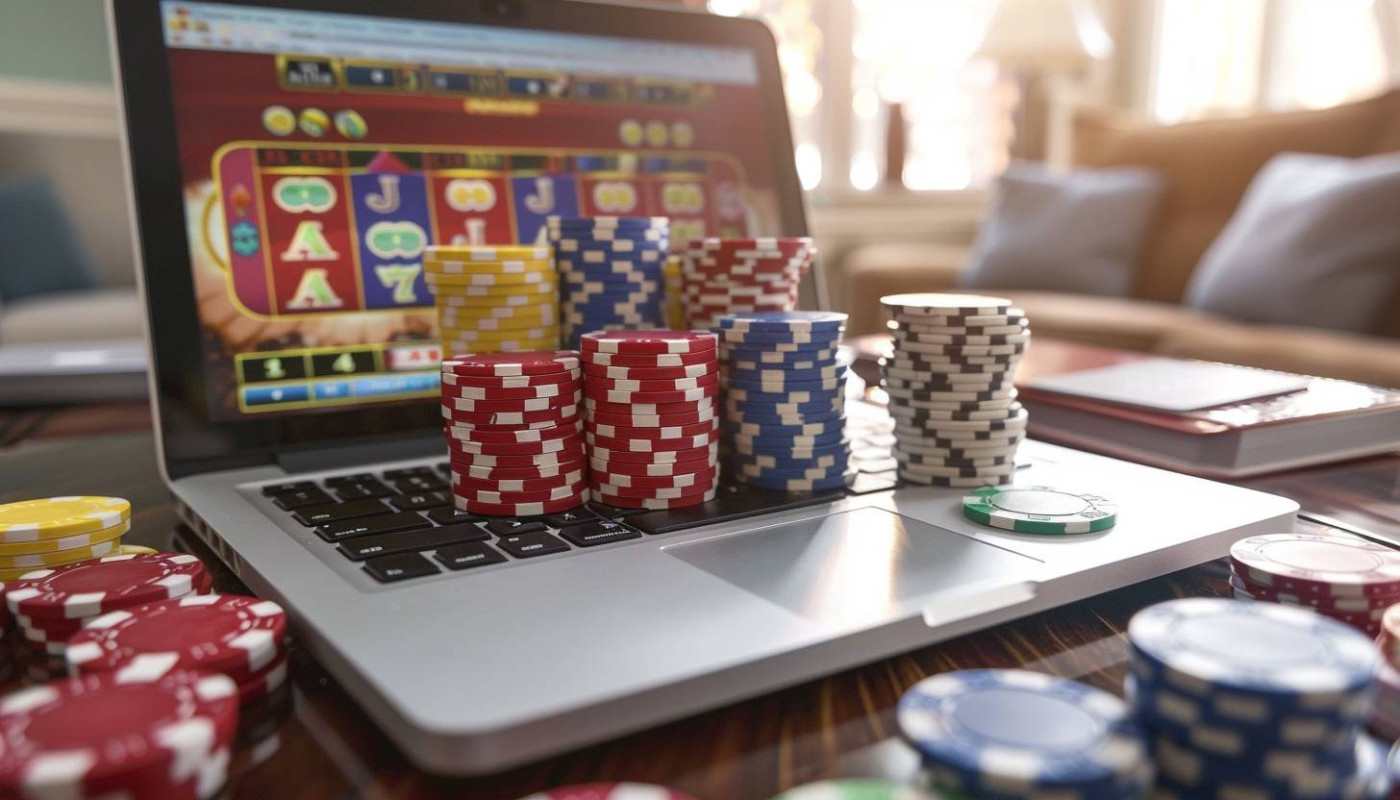
Exploring The Thrills Of Online Casino Bonuses: How To Maximize Your Gaming Experience
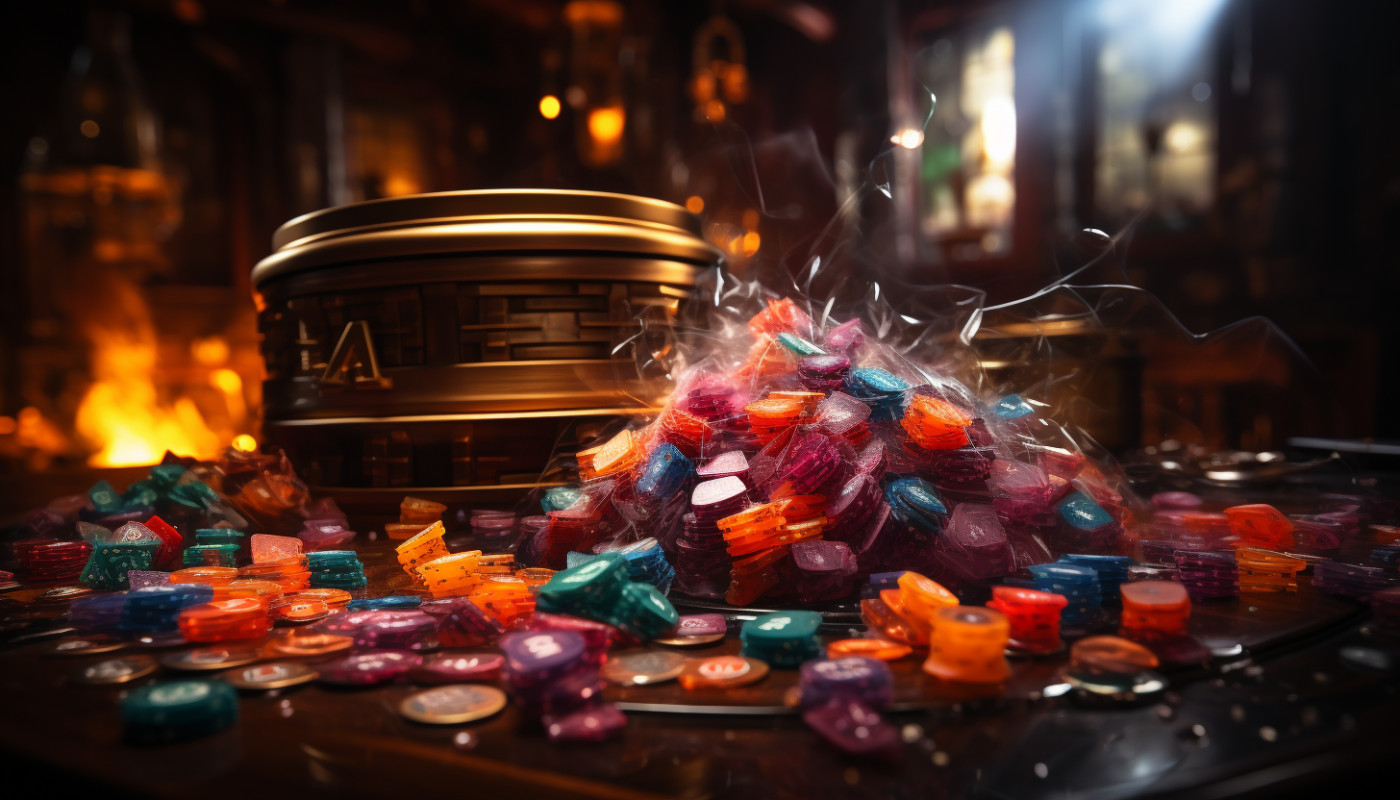
Exploring The Excitement Of Free Play Casinos: Strategies, Bonuses, And Winning Big
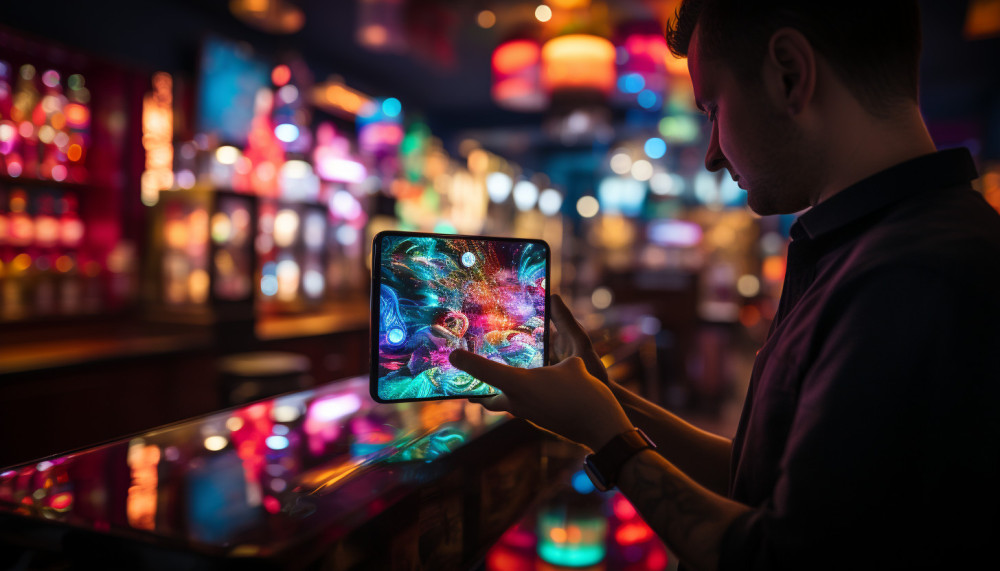
The Rise Of Mobile Gaming: How Smartphones Have Transformed The Online Casino Experience
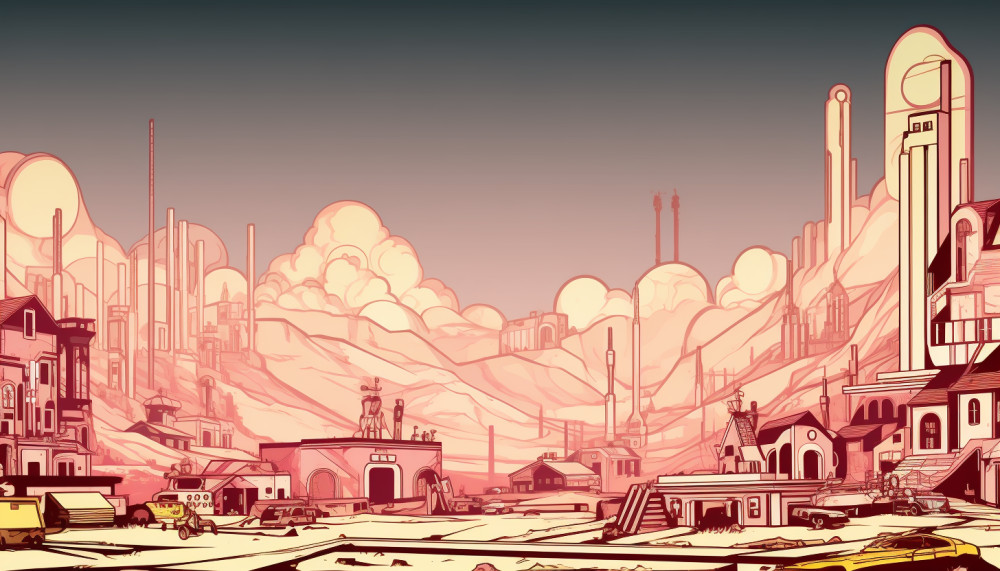
The Influence Of Fallout: New Vegas' Casinos On Modern RPG Design
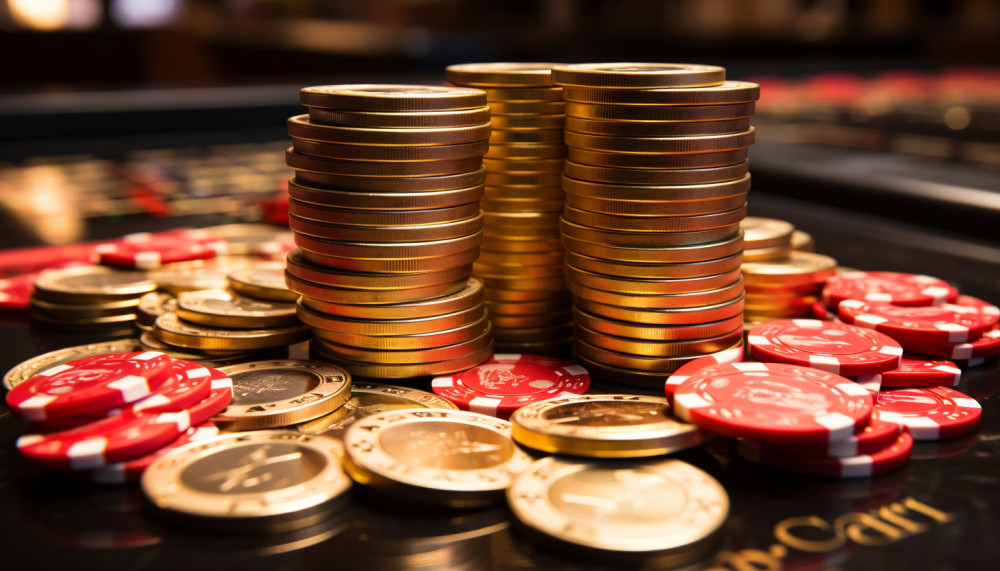
The Psychology Behind Welcome Bonuses: What Attracts Players To New Casino Sites?
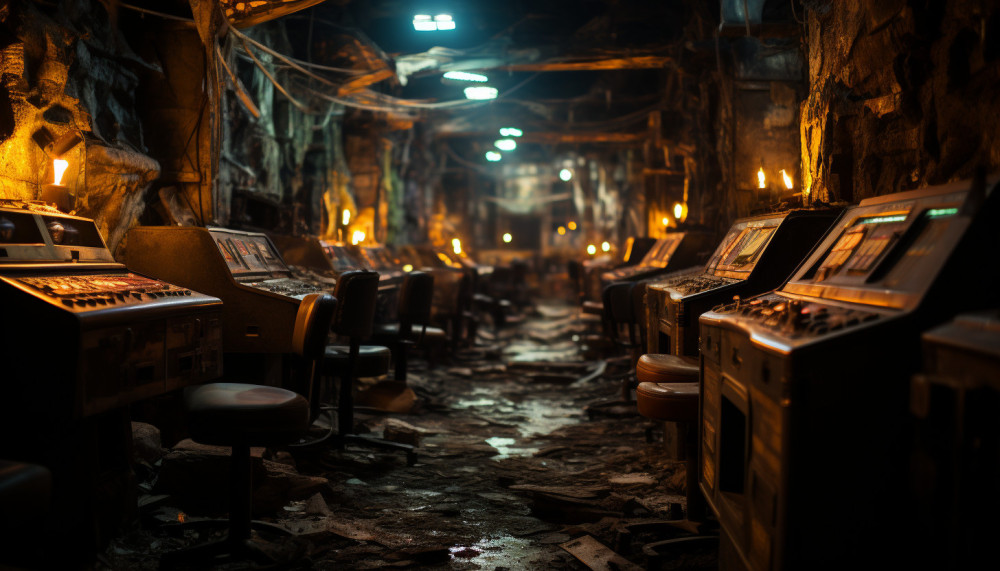